Like other products for industrial purposes wire rope requires maintenance to ensure it has a long longevity. As per experts like Viper WRL this involves lubricating the cable in order to ensure it functions properly. The motives why we lubricate wire ropes are as follows:
- The reduction of friction between each of the wire Strands
- Interior and exterior safety against corrosion
What are the Various Types of Wire Rope Lubricant?
There are two types of lubricants: coating and penetrating. The lubricant that penetrates contains solvent that transports the lubricant to the innermost part that makes up the rope. It. Then it evaporates, leaving behind a film that completely covers every strand. Lubricants coated with coatings do penetrate, but they also shield the outside and the outside of the cable against rust and corrosion. For wire ropes that have an inner fiber petrolatum or mineral oils are utilized to lubricate the core, which acts as a reservoir that provides long-lasting oil lubrication during use. For ropes with steel cores oil or grease oils are applied to the wires prior to forming them into strands in order to guarantee maximum coverage.
Different kinds of lubricants that employ different methods of application are on the market.
- Asphaltic Products: which are the most widely used lubricants, are produced from high-viscosity residual fluids. These are typically made up of an inflammable solvent to facilitate installation and better penetration in wire rope. The application of these products can take place using brushes, swabs or spray guns, however they are not suitable for high-pressure fluids. Products that are asphaltic and don’t contain a diluent solvent need heating. The resultant tacky coating often displays “dripping” issues when heated or is weak under low temperatures.
- Based on Paraffin Wax: A different class of lubricants are based on paraffin wax. It can be used with or without solvent. Solvent-free products must be melted prior to application. They are typically applied using a brush or swabs. There are a variety of kinds of greases available on the market. Some are great for lubricating wire ropes according to their composition and the methods of application.
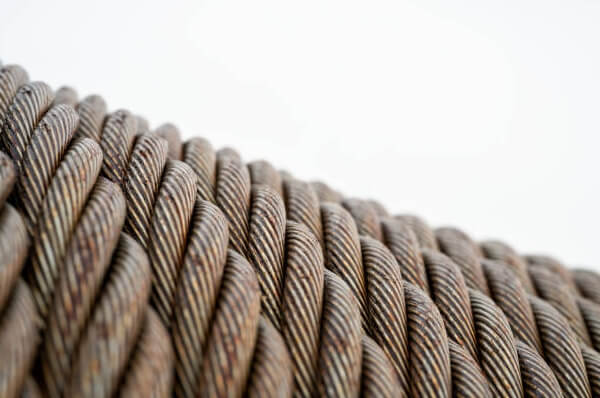
3 Factors Affect the Quality of my Wire Rope?
Corrosion: This occurs naturally that causes damage and increases loss of metal. It can be caused by fumes or humidity, high temperatures, or other factors.
Types of operations: Certain procedures put greater stress on the wire rope than other types of operations.
Wear rate: Large loads, stop/start accelerations of the cable as well as excessive use all contribute to a higher wear. Unsafe practices can result in splicing or winding that is not correct or storage conditions that are not appropriate.
Do I have to re-lubricate the Wire Rope?
Initial lubrication takes place during the process of manufacturing, however the process of re-lubricating is an excellent idea in order to increase the life for your cable rope. In fact, the lubricant used in the beginning could evaporate because of the constant stretching and the bending. It could also dry out due to the evaporation of heat.